A simple method of creating artificial muscles for use in robotics involves twisting polymer fibers around a mandrel. Although common, the process is expensive and extracting the mandrel from the coiled fibers creates excess waste.
New research, conducted in part at Texas State University, has developed an innovative new process to create artificial muscles, eliminating the mandrel entirely by plying twisted strands of polymer fiber together.
Wenting Cai, Ph.D., an assistant professor in the Department of Chemistry and Biochemistry at TXST, contributed to the research. Ray Baughman, Ph.D., director of the Alan G. MacDiarmid NanoTech Institute at the University of Texas at Dallas, headed up the international effort. The study, titled “Mandrel-free fabrication of giant spring-index and stroke muscles for diverse applications,” is published in the journal Science.
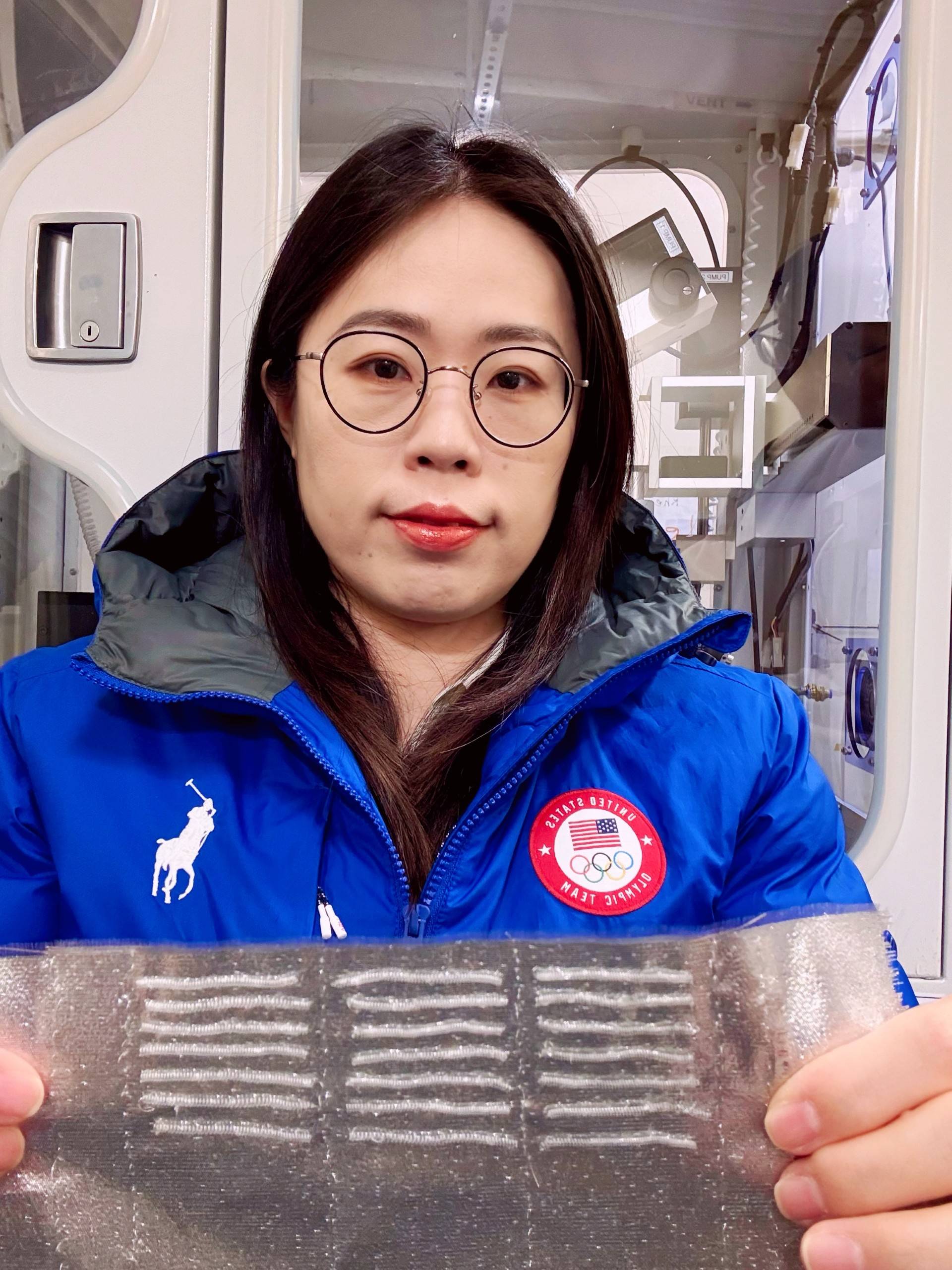
“We have demonstrated an inexpensive mandrel-free method for making springlike, thermally-driven polymer muscles that can stretch 97% of their original length and have a spring index over 50,” Cai said. “This new method can be used for fabricating artificial muscles for potential use in robots, in comfort-adjusting jackets that become more thermally insulating as the surrounding air becomes colder and as mechanical energy harvesters.”
The yarn’s functionality and mechanical properties depend on the spring index, which is the ratio of the yarn-center to yarn-center coil diameter to the diameter of the component fiber. Springs with a small spring index are tightly wound and stiffer than those with a higher index, which are more loosely wound and more flexible (videos of the mandrel-free artificial muscles can be found here).
Until now, no process has been able to produce large-spring-index yarns other than to dissolve the mandrel after muscle coiling, which is expensive and wasteful.
“Our inexpensive mandrel-free method provides an important way to fabricate high-spring-index yarn and to address applications where large strokes are required, but the delivered work can be small,” Cai said. “The mandrel-free fabrication process involves inserting twist into individual fibers at a level below the twist, causing them to coil back on themselves, then plying the twisted fibers to create springlike coils. During plying, each fiber serves as a mandrel for other fibers.
“Our technology enables the muscle’s spring index, and corresponding tensile stroke, to be continuously varied in any desired manner over the muscle’s entire length, merely by changing the plying twist density during manufacture,” she said. “When heated and cooled, these muscles can significantly contract and elongate due to their large spring index.”
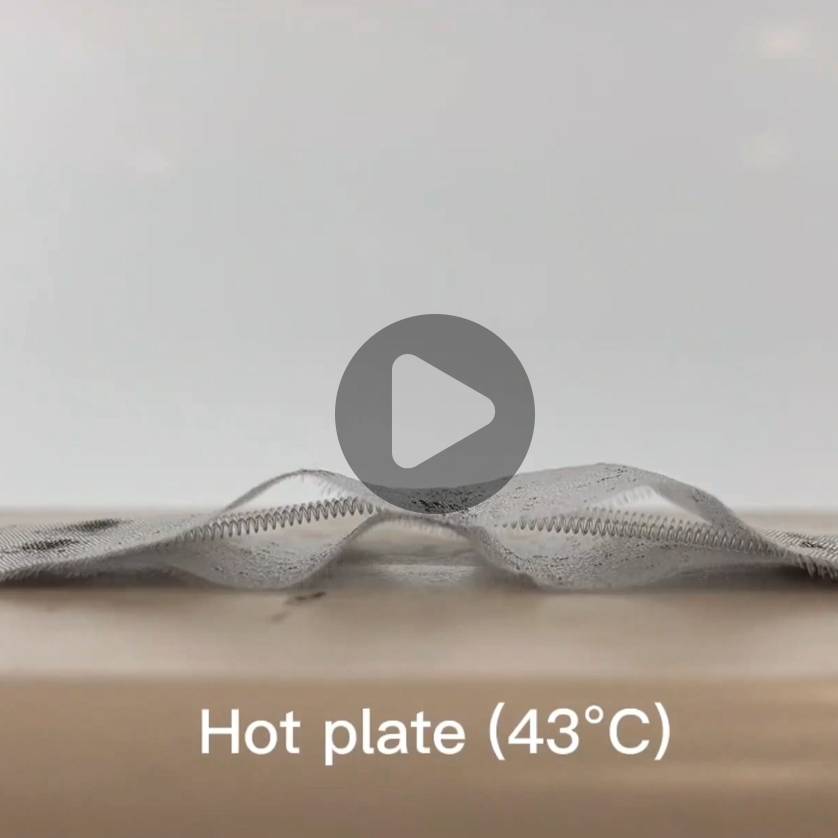
The mandrel-free method enables the spring index to be varied along a muscle’s length. The team demonstrated a muscle having multiple spring indices by incorporating it into a crawling robot. The high-spring-index sheath-core muscle is made of CNT-wrapped polymer fibers. The precise expansion and contraction of the muscle is driven by heat, which may be provided by applying electricity, solvents or other electrochemical means—a trait desirable for most robotic applications.
The team also used the mandrel-free method to make high-spring-index carbon nanotube yarns, which could be used to harvest mechanical energy or as self-powered strain sensors.
One application for the innovative technology that consumers could directly encounter is comfort-adjusting jackets that automatically open large, thermally insulating pores as the ambient temperature becomes uncomfortably cold. Commercialized jackets containing mandrel-coiled artificial muscles were worn by members of the U.S. team at the 2022 Winter Olympics in Beijing. However, the jackets were subsequently discontinued due to the expensive mandrel-wrapped process. The new mandrel-free method for making high-spring-index coiled fiber avoids this major problem and could lead to the commercialization of new comfort-adjusting jackets.