Texas State’s Makerspace Creates ‘Ear Savers’ on 3D Printers
Steve Ulfelder | May 28, 2020
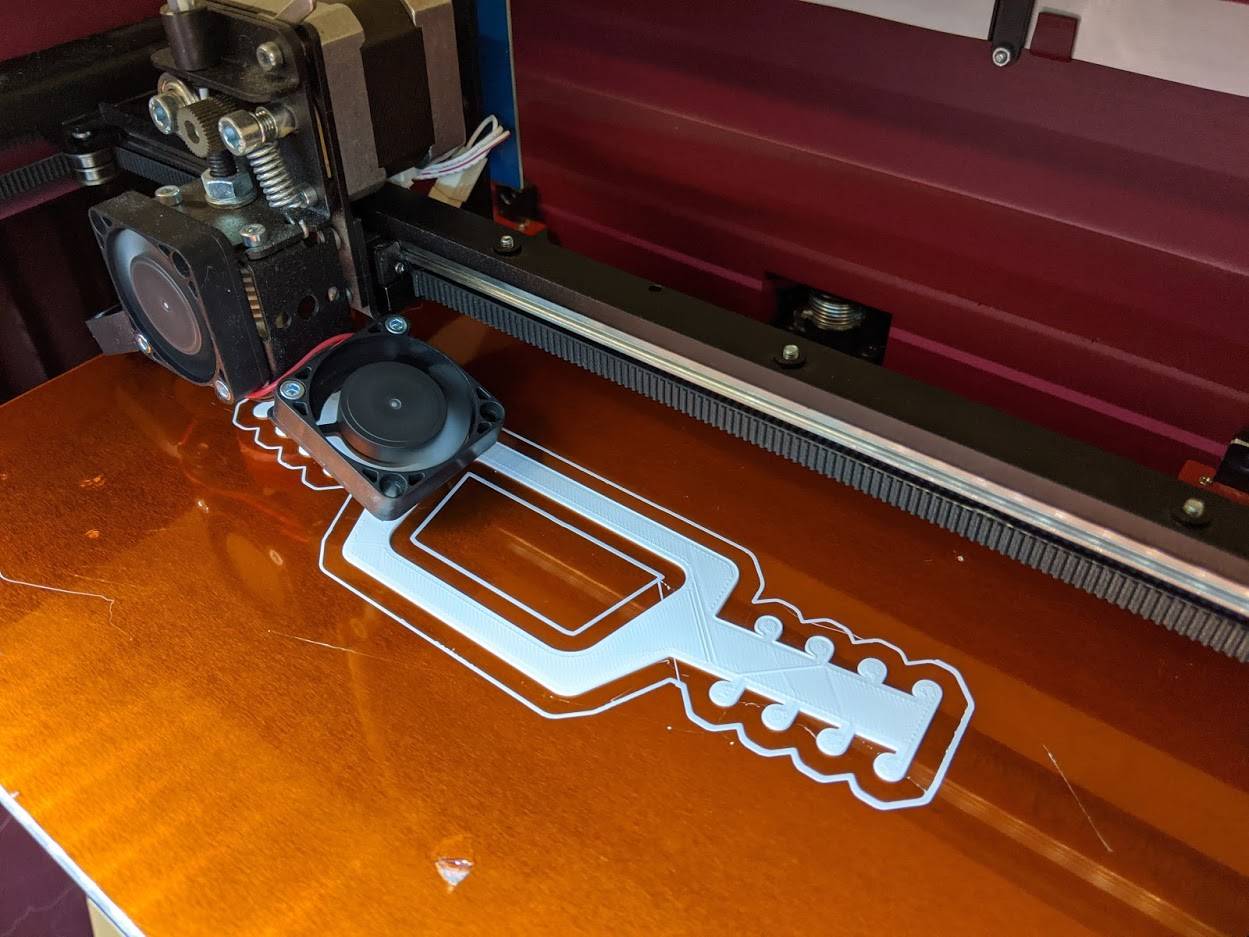
The masks now worn by millions worldwide have potentially life-saving benefits. However, they have drawbacks too—especially for those law enforcement and healthcare professionals who must wear them for hours on end. The elastic bands that secure masks chafe the ears after a while, leading to pain and even infections.
In a bid to help, students and professionals at Texas State’s Ingram Hall Makerspace (IHM) are using material that would otherwise go to waste, along with three-dimensional printers and ingenuity, to conceive, prototype, test and produce thousands of “ear savers.” Already, these pain-saving gizmos have been distributed to university police, student health center employees, and others on the front lines—and the inventors want to give away even more.
The IHM is an 8,000-square-foot collaborative academic space for creating, learning, inventing, and practicing the free exchange of ideas. “We’re training students, helping them undertake class projects,” says John Ivey, IHM director. Problem-solving is the focus, with students learning to prototype and react quickly to market needs.
The space features approximately 60 3D printers, each of which is equipped with a spool of PLA filament—the material of which objects are created. This filament is prized by engineers for its low cost and malleability, but when it sits for extended periods, it absorbs moisture from the air and becomes useless.
That appeared to be the PLA filament’s fate when, in March, the COVID-19 pandemic forced the Makerspace to shut down. Matt Candelas had other ideas.
Lemonade from lemons
Candelas earned his bachelor’s degree in Mechanical Engineering Technology in December and is now pursuing a master of science in technology management. As the coronavirus spread, Candelas and other Texas State students immediately considered addressing a global shortage by printing masks. However, the PLA filament was poorly suited to that application. “It’s rigid,” Ivey says, “it’s just not a material you want on the front of your face.”
Candelas and his cohorts were undeterred. They’d heard workers at the student health center complaining about strain on their ears from wearing surgical masks all day. “My younger brother,” Candelas says, “who just graduated from the nursing program at Texas State, had sent me a picture of a 3D-printed ear saver he’d been given a few days prior.”
That was the “Aha” moment.
Taking the strain
If simplicity is the heart of a great invention, the device widely known as an ear saver is truly brilliant. It’s simply a piece of plastic about 6 inches long, with sets of hooks at each end. The device is worn on the back of the neck. The elastic on masks hooks over the device ends, removing strain from the backs of the ears.
With the end product identified, it was time to act. Candelas used computer-aided design software and a 3D printer to create a few samples. Those were rushed to the student health center, where workers requested a longer strap to accommodate larger heads.
That request was met, and another test ensued. There was one more request, this time for a sort of hoop shape through which long hair could be pulled.
That did the trick, Candelas says. “On the third iteration, we had a design the medical staff approved of and was easy enough to manufacture quickly.” One advantage of 3D printing is speed; the prototyping phase required only a few days “because we could print a new design in about 20 minutes and test it immediately,” he says.
Now it was production time, and Ivey—who had also been involved throughout the prototyping—took over. He had figured out how to shift Makerspace printers so that 20 could run simultaneously with appropriate social distancing in place. Soon the hall was humming. Everybody was anxious to do their part; Sarah Rivas, an administrative assistant, has remained at Ingram Hall as an essential worker, “So we’ve got her running a rack in her office,” Ivey says.
So far, more than 3,000 ear savers have been manufactured. Ivey has distributed more than 1,000 internally and wants to give away even more; he stresses that Texas State employees and departments that want to increase their comfort should contact him.
Ivey and Candelas agree that filling a need during a crisis, with material that would otherwise go to waste, exemplifies all that the Makerspace can be. “I enjoy the collaboration, and I think everyone is just happy to feel like we’re doing our part,” Candelas says. “It’s just fantastic to enable projects like this one,” Ivey adds. “You love seeing students who can tackle problems this way.”
Share this article
For more information, contact University Communications:Jayme Blaschke, 512-245-2555 Sandy Pantlik, 512-245-2922 |